GREEN HYDROGEN PLANT DESIGN & ENGINEERING COURSE
10
modules
Flexible
learning program
1 on 1
Mentor Ship
3 Months
Duration
Live Projects
experience
COURSE OVERVIEW
This comprehensive course equips you with the knowledge and skills to design and engineer efficient green hydrogen plants. We’ll explore:
- The Fundamentals: Understanding the role of hydrogen in the energy transition, its production methods (green vs. traditional), and applications across various sectors.
- Renewable Energy Integration: Learning how to integrate renewable energy sources like solar and wind to power your green hydrogen plant.
- Electrolyzer Selection & Sizing: Choosing the optimal electrolyzer technology – PEM, Alkaline, or SOEL – based on your project’s specific needs.
- Hydrogen Storage Solutions: Exploring diverse methods for safe and efficient hydrogen storage, including compression, cooling, and novel options like metal hydrides and ammonia.
- Plant Design & Engineering: Delving into the technical aspects of green hydrogen plant design, covering aspects like piping systems, compression systems, safety considerations, and electrical systems.
- Economic & Market Analysis: Understanding the financial viability of green hydrogen projects, including cost considerations, economic modeling tools, and potential market opportunities.
- Real-World Examples: Learning from case studies of existing green hydrogen projects to gain valuable insights for your own designs.
Completing this course will charge you for:
- Understand fundamentals of hydrogen, the production process, application of hydrogen and international policies and laws
- Learn from industry experts on development and implementation of latest technologies in hydrogen based on hydrogen pricing, markets, and other economic factors
- Design a green hydrogen plant: Apply your knowledge to create a safe, efficient, and sustainable plant layout.
- Select and size key equipment: Choose the optimal electrolyzer, storage tanks, and other components for your project.
- Integrate with renewable energy: Ensure your plant leverages clean energy sources like solar and wind
- Evaluate project economics: Analyze the financial feasibility of your green hydrogen project.
- Process of electrical energy generation from hydrogen by using fuel cell technology
Who is the course for?
- Engineers who wants to switch their department/unit to Substation Engineering department/unit in their Company
- Engineers from state Electricity Boards, Power Utilities/ Corporations
- Graduate Engineers from Academic institutions
- Pre-Final Year & Final Year Engg. Students
- R & D organizations, Research Scholars
- Engineers seeking to specialize in green hydrogen plant design.
- Professionals in the renewable energy sector looking to expand their knowledge of hydrogen production.
- Anyone interested in understanding the future of clean energy and the role of green hydrogen.
learning path
This introductory module opens the door to the exciting world of green hydrogen production and its diverse applications across various industries. As we transition towards a cleaner energy future, green hydrogen – produced using renewable energy sources – is poised to play a vital role.
Hydrogen: Powering Industries and Transportation
- The Use of Hydrogen in Industries
- Oil Refineries
- Petrochemicals
- Chemicals Industry
- Hydrogen for Mobility
- Fuel Cell Electric Vehicles (FCEVs)
Prioritizing Safety in a Hydrogen Ecosystem
- Hydrogen Safety
Current Engineering Practices in Green Hydrogen Production
- Electrolysis
- Balance of Plant (BoP) Systems
Looking Ahead: The Future of Green Hydrogen
- Emerging Applications
- Research and Development
- Methodology of Lower Cost Hydrogen Production & Source of Power Supply
- Economies of Scale
- Electrolyzer Technology Advancements
- Renewable Energy Price Fluctuations
- Renewable Energy Integration: Powering Electrolysis
- Production from Solar Power Plant Energy
- Production from Wind Energy
- Selection of Back-Up Power Source
- Current Engineering Practices in Cost Reduction
- Optimizing Electrolyzer Stack Design
- Leveraging Renewable Energy Auctions
- Looking Ahead: Cost Reduction Strategies
- Emerging Technologies
- Policy and Regulatory Landscape
- Renewable Energy Source Sizing
- Solar Photovoltaic (PV) System Sizing
- Wind Turbine Selection
- Hydrogen Production Equipment Load Calculation
- Matching Renewable Capacity to Hydrogen Demand
- Site Selection for Optimal Renewable Energy Capture
- Solar Irradiation
- Wind Speed and Direction
- Land Availability and Regulations
- Hydrogen Plant Location Considerations
- Proximity to Water Source
- Distance to Hydrogen Demand Centers
- Grid Connection Availability
- Electrical Network Integration
- Power Conversion Systems
- Grid Interconnection Standards
- Energy Storage Considerations
- Smoothing Renewable Energy Output
- Hydrogen Production During Peak Demand
Electrolyzers are the workhorses of green hydrogen production, splitting water molecules using renewable energy. This module equips you with the knowledge to select and size the optimal electrolyzer for your plant’s needs.
Types of Electrolyzers and Capacity Sizing
- Polymer Electrolyte Membrane (PEM) Electrolyzers: A popular choice known for their high efficiency and fast startup times.
- Alkaline Electrolyzers (AEL): A mature technology known for their durability and ability to handle impure water sources.
- Solid Oxide Electrolyzers (SOEL): A high-temperature technology offering high efficiency and potential for waste heat utilization.
PEM vs. Alkaline Electrolyzers: Choosing the Right Technology
- Desired Hydrogen Production Capacity: PEM electrolyzers are better suited for smaller-scale plants, while AELs can handle larger capacities.
- Water Quality: AELs tolerate a wider range of water quality compared to PEM electrolyzers.
- System Startup Time: PEM electrolyzers offer faster startup times than AELs.
Solid Oxide Electrolyzers: Exploring Next-Generation Technology
- High Efficiency: SOELs boast the potential for the highest efficiencies among electrolyzer types.
- Waste Heat Integration: The high operating temperature of SOELs allows for waste heat utilization in other plant processes.
- Technical Maturity: SOEL technology is still under development compared to PEM and AEL options.
Key Electrolyzer Selection Parameters
- Current Density: The amount of current per unit area of the electrolyzer, impacting efficiency and hydrogen production rate.
- Operating Pressure and Temperature: These factors influence efficiency, capital costs, and maintenance requirements.
- Hydrogen Purity: The desired level of hydrogen purity based on end-use applications.
- System Footprint and Weight: Considering space constraints and transportation requirements for the chosen electrolyzer.
Hydrogen and Oxygen Separation
- Hydrogen Separator: Ensures the purity of produced hydrogen by separating it from oxygen generated during electrolysis.
- Oxygen Separator: Allows for safe collection and potential utilization of the co-produced oxygen.
Water Quality Considerations for Electrolyzer Operation
- Feed Water Quality Requirements: The specific water quality specifications for different electrolyzer technologies.
- Water Treatment Options: Methods for pre-treating water to meet the requirements of your chosen electrolyzer.
Hydrogen Tank Specifications and Capacity Calculation
- Material Selection: High-pressure composite vs. metallic options
- Pressure Rating: Impact on storage capacity and safety
- Temperature Range: Compatibility with process conditions
- Capacity Calculation: Volume based on pressure and storage duration
Selecting the Right Hydrogen Storage Tank
- Application Requirements: Matching pressure, capacity, and material
- Safety Regulations: Adherence to industry standards
- Space and Transportation Considerations: Physical size and weight
Key Selection Parameters for Hydrogen Tanks
- Maximum Pressure Withstand (MPa): Storage density considerations
- Temperature Range (°C): Material selection and insulation needs
- Storage Capacity (kgH2): Balancing pressure and usage duration
- Tank Material: Weight, durability, and hydrogen compatibility
- Design Temperature (°C): Efficiency and potential temperature control
Mitigating Hydrogen Storage Tank Leakage
- Leak Detection Systems: Technologies for early leak identification
- Material Selection and Maintenance: Minimizing leakage risks
- Safety Regulations and Practices: Leak prevention measures and response procedures
Piping Arrangement Architecture
- Layout considerations for efficient hydrogen flow throughout the plant
- Minimizing pressure drops and ensuring safety through proper pipe sizing and routing
Compressor Selection for Hydrogen Service
- Types of compressors suitable for hydrogen compression (e.g., reciprocating, centrifugal)
- Matching compressor type and capacity to desired pressure increase and hydrogen flow rate
- Material selection for compatibility with hydrogen
Pressure Control Components
- Pressure Relief Valves (PRVs): Protecting equipment from overpressure events
- Pressure Indicators: Monitoring hydrogen pressure at key points in the system
- Isolation Valves: Enabling controlled isolation of sections of the piping for maintenance
Hydrogen Gas Inlet and Outlet Considerations
- Selection of valves suitable for hydrogen service and pressure rating
- Ensuring proper flow direction and control for efficient hydrogen movement
Hydrogen Storage Tank Integration
- Determining optimal tank placement considering safety, efficiency, and piping lengths
- Selecting tank size based on required hydrogen storage capacity and pressure
Challenges of Direct Hydrogen Transport
- Addressing the low volumetric density of hydrogen gas for efficient transportation
- Safety considerations for high-pressure gaseous hydrogen pipelines
Utilizing Intermediate Carriers for Hydrogen Transport
- Ammonia (NH3) as a hydrogen carrier:
- Production from green hydrogen and nitrogen
- Cracking ammonia to release hydrogen at the destination
- Hydrocarbons as hydrogen carriers:
- Liquid Organic Hydrogen Carriers (LOHC) for safe and efficient transportation
- Chemical processes for hydrogen release from LOHC molecules
Selecting the Optimal Intermediate Carrier
- Infrastructure availability for both production and utilization of the chosen carrier
- Safety considerations throughout the transportation chain
- Energy efficiency and lifecycle assessment of each carrier option
Case Studies: Hydrogen Transport Projects
- Exploring real-world examples of transporting hydrogen using intermediate carriers
- Highlighting the technical and economic considerations of these projects
Electrical Equipment Switchgear Selection
- Selecting appropriate switchgear (e.g., circuit breakers, isolators) for safe and reliable operation of hydrogen production equipment
- Matching switchgear ratings to equipment power requirements and fault current levels
Electrical Cabling Design and Sizing
- Determining cable sizes for various electrical loads (e.g., electrolyzers, pumps) based on current carrying capacity and voltage drop considerations
- Selecting cable type suitable for the operating environment (e.g., temperature, moisture resistance)
Hydrogen Plant Lighting Design
- Implementing appropriate lighting solutions for different areas of the plant (e.g., control room, maintenance areas) considering safety regulations and energy efficiency
Earthing System Design for Hydrogen Safety
- Establishing a safe and effective earthing system to prevent electrical hazards and ensure equipment protection
- Following industry standards for hydrogen plant earthing design and maintenance
Auxiliary and Main Power Supply Systems
- Selecting and sizing auxiliary power systems for critical equipment and control systems
- Designing the main power supply system to ensure reliable electricity delivery to the plant, considering grid connection and potential backup options
Fundamental Economic Considerations for Hydrogen Projects
- Capital Expenditure (CapEx): Evaluating costs associated with plant design, construction, and equipment.
- Operational Expenditure (OpEx): Analyzing ongoing costs for feedstock, electricity, maintenance, and labor.
- Levelized Cost of Hydrogen (LCOH): Understanding the average cost of producing hydrogen over a project’s lifetime.
Resources for Economic Modeling and Data
- Identifying relevant databases and tools for hydrogen project cost estimation and techno-economic analysis (TEA).
- Exploring resources from government agencies, industry associations, and research institutions.
Hydrogen End-Use Cost Considerations
- Transportation costs: Factoring in pipeline infrastructure, liquefaction, or alternative carrier options.
- Hydrogen storage costs: Evaluating storage tank requirements and associated expenses.
- Hydrogen dispensing infrastructure costs: Considering refueling station development or industrial hydrogen delivery systems.
Cost Expectations and Considerations
- Projected cost reductions for hydrogen production and infrastructure based on technological advancements and market growth.
- Factors influencing project economics: Government incentives, carbon pricing, and renewable energy costs.
Policy and Technological Uncertainties
- Addressing potential policy changes impacting project viability.
- Navigating uncertainties associated with emerging hydrogen technologies.
Hydrogen Safety Regulations and Standards
- Understanding safety requirements for hydrogen production, storage, transportation, and utilization.
- Following industry standards and regulations for safe plant design, operation, and maintenance.
Electrical Power Distribution Scheme Preparation
- Applying electrical load calculations to design a safe and efficient power distribution system.
- Selecting appropriate transformers, switchgear, and cabling for the plant’s electrical needs.
One-Line Diagram Development for a Hydrogen Plant
- Creating a simplified representation of the plant’s electrical power flow.
- Highlighting key electrical components like transformers, breakers, and buses.
Hydrogen Plant Layout Design Considerations
- Optimizing equipment placement for efficient process flow and maintenance access.
- Considering safety regulations and separation distances between equipment.
Case Studies: Exploring Real-World Green Hydrogen Projects
- Analyzing existing green hydrogen plants to understand design choices, challenges, and best practices.
- Learning from case studies of varying project sizes, locations, and applications.
Above Course available on Regular, Weekend basis For Working Professionals in Online Mode.
A BETTER CHOICE
Why learn with 50Hz-Academia?
We are dedicated to ensuring that you adopt world-class professional engineering practices and gain skills that you can immediately implement in the workforce.
This course has been designed to provide you the practices of current engineering process used in Power & Electrical industry based on industry standard.
What people are saying
“I was looking for a Substation Designing Course to expand my career horizon. A friend of mine suggested to learn from 50Hz-academia online courses and it really worked for me.”
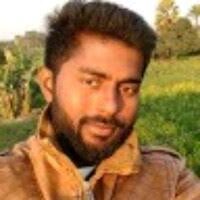
“This course was a breakthrough in my knowledge of power industry. The modules are comprehensive and of great quality, engaging and interactive.”

Companies Have Hired 50Hz- Academia Learners
FIND OTHER COURSES YOU NEED
SOLAR POWER PLANT DESIGN & ENGINEERING COURSE
This course has been developed to meet the requirements of the National Standards.
DIGITAL SUBSTATION DESIGN & ENGINEERING COURSE
This course has been designed to learn about engineering process to Digitized Substation.
GREEN HYDROGEN PLANT DESIGN & ENGINEERING COURSE
This course explains the needs, processes & applications of green hydrogen as a energy revolution.
SUBSTATION DESIGN & ENGINEERING COURSE (11KV TO 765KV)
The Program has been designed to learn the designing of Complete Substation.
BATTERY STORAGE SYSTEM DESIGN & ENGINEERING COURSE
The Program has been designed to learn the designing of Battery Storage System.
POWER SYSTEM PROTECTION & RELAY COORDINATION COURSE
The Program has been designed to learn the Power System Protection & Numerical Relay Coordination study.